Post-stabilization is the key to success
Post-stabilization of recyclates is crucial for quality assurance in the plastics recycling industry. Customized stabilizer systems can neutralize oxidative damage, which increases the reusability of polyolefin recyclates. This leads not only to better product properties, but also reduces the consumption of resources and promotes the sustainable use of plastics.
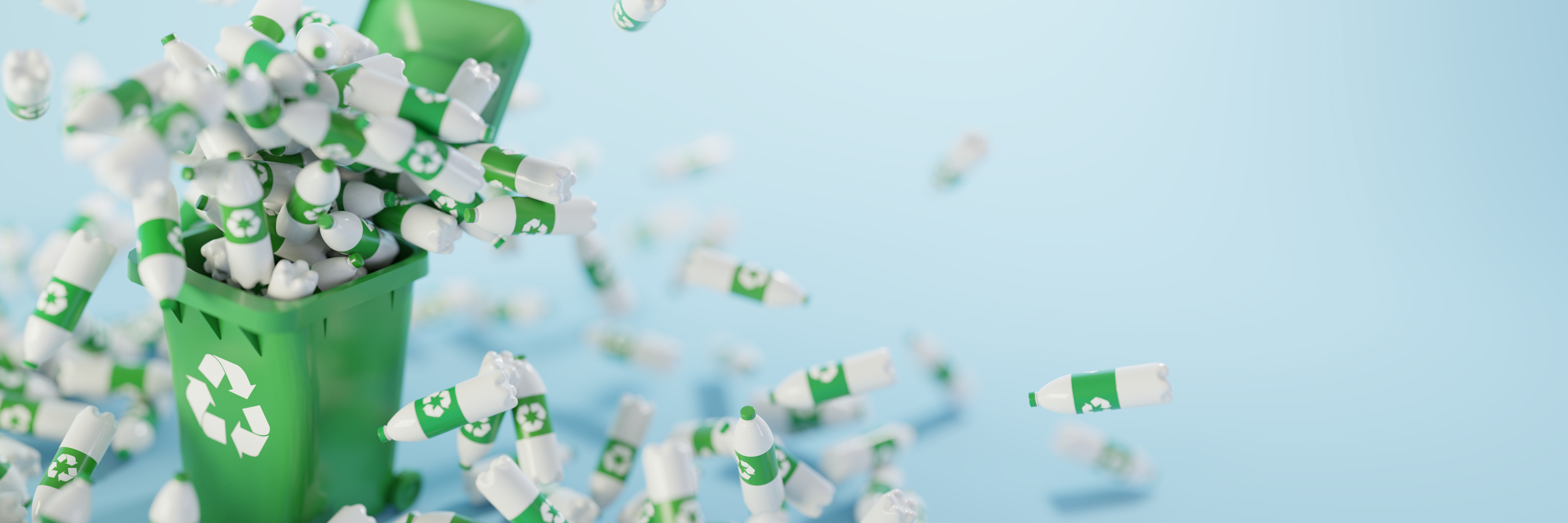
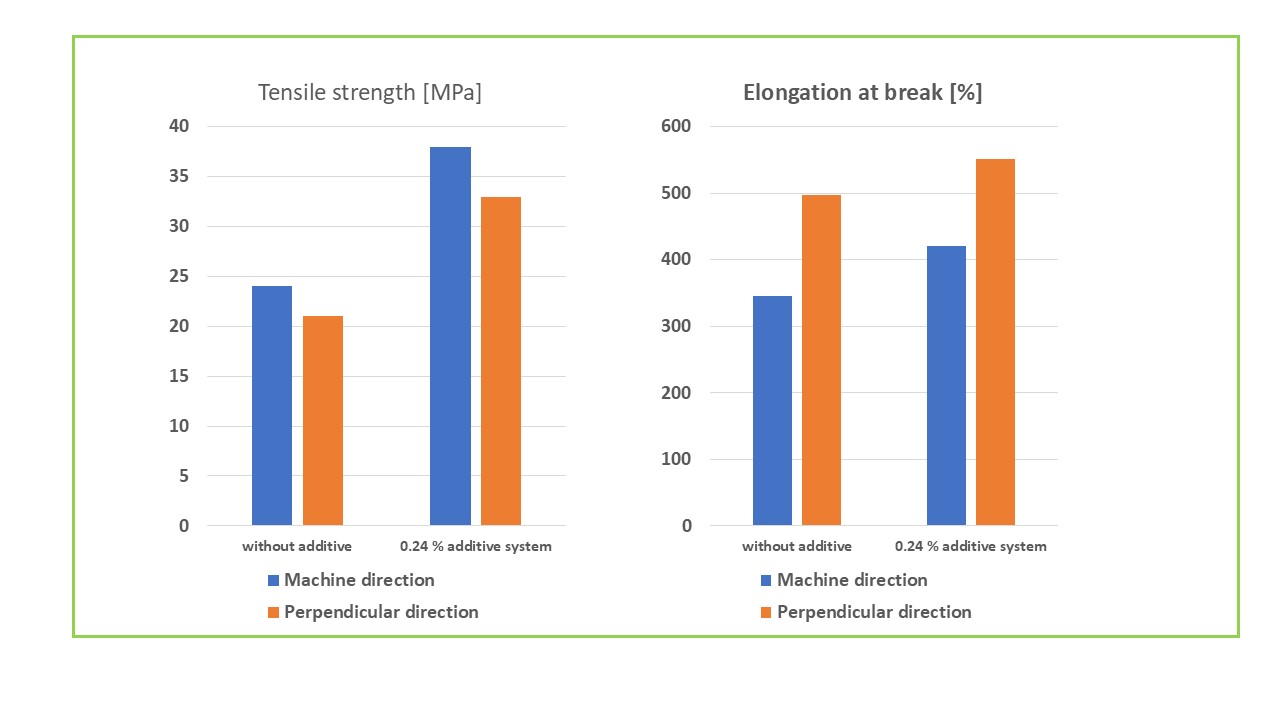
The mechanical recycling of plastics is energetically and ecologically the first choice in a successful plastic circular economy. To survive in the market, recyclates must have the same high-quality properties as new products. However, plastics usually show deficits after a first successful use: the recyclates are oxidatively damaged, the processing properties have changed and the necessary stability for a new application is no longer given. The use of customized additives is then unavoidable.
Of course, functioning collection systems and sufficiently good cleaning, sorting and separating processes are important prerequisites for suitable material flows. After impurities, composition and state of aging have been determined, new formulations can be developed with the addition of selected additives. Only production waste is an exception here and is usually returned unchanged to the production process in subordinate proportions.
The entire range of additives is available to improve the quality of recyclates, in particular stabilizer systems, compatibilizers, reactive molecules to “repair” pre-existing damage and odor The costs of the additives used are always a factor, but they can often be offset by increased productivity, more consistent production, improved material qualities and an expanded range of applications for the recyclate.
Post-stabilization is the main method for improving the quality of polyolefin recyclates. New plastics based on polyolefins cannot be processed or used without the addition of antioxidants, as these protect the polymer chains from oxidative (and/or photo-oxidative) damage. However, the stabilizers are consumed when they perform their protective function and are therefore missing in a recyclate. The used stabilizer quantity from the first use must therefore be replaced. Another challenge is the transition from a short-term use, such as packaging, to a long-term use. In such cases, the starting material is not prepared for the new intended use.
Within the framework of the CCPE, the Fraunhofer LBF has devoted itself to the post-stabilization of recyclates and developed a new generation of stabilizer systems tailored to the special requirements of recyclates. Recyclates, in particular post-consumer polyolefin recyclates, usually show pre-existing damage due to oxidation.
From a chemical point of view, there is an increased concentration of ketone groups, hydroperoxides and acid groups in the polymer chains. These groups are initiator sites for further accelerated damage to the recyclate. The newly developed stabilizer systems not only provide very good stabilization during processing and in (long-term) use, but also “neutralize” the initial damage at the same time. Components continue to complex transition metals, which often occur as impurities in recyclates, and thus neutralize their pro-oxidative effect. Additional effects can include improved mechanical properties and fewer defects, e.g. in films (Fig.). Due to the recyclate-specific effect, only low additional concentrations are required compared to conventional standard stabilizers. Possible recyclate markets include polypropylene, especially injection molding applications, HDPE, LDPE/LLDPE film grades, but also polyolefin blends. Since the composition of these new stabilizer systems, which have been specially developed for recyclates, can be flexibly adapted, products can also be optimized for various recyclate streams. Please feel free to contact us about this.